7 Benefits of a Warehouse Management System
When it comes to running an Ecommerce business, there are a lot of moving parts. Without someone—or something—tracking it all, things can slip through the cracks. This is where a Warehouse Management System (WMS) comes in handy. A WMS benefits your business by watching over the business, tracking key data, and providing crystal clear visibility of operations.
"Investing in a WMS isn't about adding complexity—it's about simplifying operations, improving efficiency, and giving businesses the control and operational insight they need to grow.” - Rick Nelson, CEO, The Fulfillment Lab |
In addition to tracking inventory, order and fulfillment status, and employee productivity, there are numerous other advantages of a warehouse management system, seven of which we’ll discuss in this blog. We’ll also explore what a warehouse management system is, the key features a quality WMS must have, and tips on how to choose a WMS for your business.
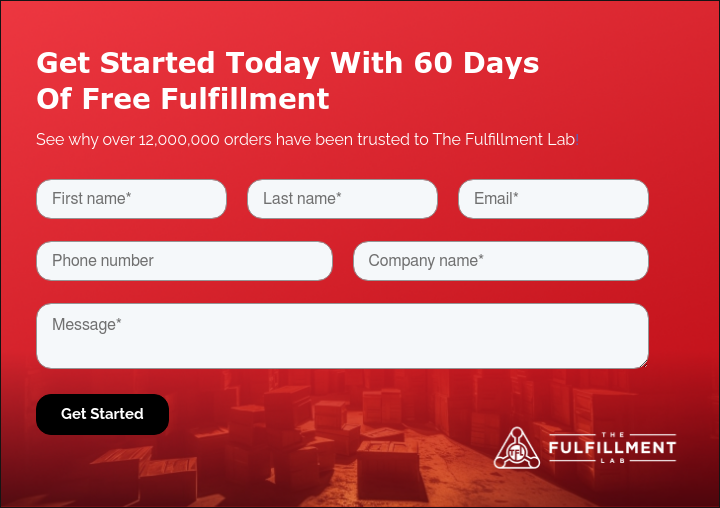
What Is a Warehouse Management System?
Warehouse management systems are software programs that have been designed to optimize the warehouse and streamline procedures. In short, a warehouse management system (WMS) helps ensure that goods and materials move along in the most efficient and cost-effective way.
It does this by keeping an eye on:
- Warehouse design
- Inventory tracking
- Order fulfillment
- Receiving and storing inventory
- Shipping
- Labor management
- Yard and dock management
- Returns management
- Reporting
The purpose of any WMS, first and foremost, is to offer transparency across all warehouse operations and provide insight into its effectiveness and efficiencies as well as provide analytical insights into how the warehouse is being run.
The growing versatility and capabilities of modern WMS systems make them increasingly popular. The global warehouse management system market is set to grow from $4 billion in 2024 to $8.6 billion by 2029, with a 16.3% annual growth rate.
Moreover, consumers are now spending more on e-commerce purchases than ever before. As of 2023, 63% of consumer dollars are spent on online purchases, while just 37% go towards in-person purchases of goods. As this trend continues, the reliance on warehousing services, and the WMS systems that operate them, will undoubtedly increase as well.
Top 7 Benefits of a Warehouse Management System
1. Improved Communication
86% of executives and employees say poor collaboration and communication is the root cause of workplace failures. In a warehouse environment, poor communication can cause shipping delays, order accuracy errors, missed deadlines and result in poor customer satisfaction as well as higher return rates.
However, the right WMS software can improve communication among team members by providing greater transparency and insight through a centralized system. This allows teams to track orders, fulfillment times, shipping procedures, and customer feedback in real-time, cutting down on confusion, human error, and bottlenecks that result in frustrated customers.
2. Accurate Inventory Management
Good inventory management is essential to make sure inventory is where it needs to be, in good condition, and there is the right amount or products on the shelf. Poor inventory management costs businesses millions each year.
The global retail industry loses $1.75 trillion a year due to out-of-stock inventory, and overstocks increase overhead costs unnecessarily.
WMS software helps prevent stock outs and over stocks from happening with automations that track inventory location, volume, and more. A good WMS can even notify the appropriate stakeholders when inventory levels are low, about to expire, or other essential product quality alerts.
3. Improved Product Safety and Security
As warehouse usage grows, so does the number of people working in them and the amount of safety and security incidents happening within them. Startlingly, there are more non-fatal workplace accidents occurring in warehouses than any other industry.
WMS systems can help keep employees and goods safer by tracking the movement of items and ensuring proper handling procedures are followed. They also assist in monitoring safety protocols, identifying potential hazards, and providing real-time alerts, ultimately reducing the risk of accidents and improving overall warehouse safety and security.
4. Scalability as Your Business Grows
The goal of most businesses is to continue to grow, making a WMS a necessity. Without one, as your business expands, warehouse and inventory management will become even more complicated, labor intensive, and likely be unable to keep up with demand.
Fortunately, a great benefit of a warehouse management system is how it can easily grow with you, allowing you to scale without skipping a beat. Cloud-based WMS in particular offers the flexibility, availability, and capacity to evolve in tandem with your operations and can even make international warehouse management easier than you think.
5. Faster Order Fulfillment
Today, consumers want immediate gratification, which is why expedited shipping is so important. Studies show that 3 days or less is the most acceptable timeframe for delivery. However, if you can offer same-day or 1-day delivery, you should.
So, if you’re going to compete with the Amazons and Walmarts of the world, or even the guy next door, a quality WMS can help. Efficient warehouse management software enables your team to process and fulfill orders much faster, reducing fulfillment latency and processing times. The end result of this being happier customers who are willing to return to your store for more!
6. Lower Processing Costs
Faster order fulfillment means less time and resources are spent on every order. When you increase fulfillment speeds, there’s a bonus benefit: you reduce process costs, oftentimes significantly.
The right WMS is paramount to creating these cost and time savings. Be sure you calculate your customer cost per order before implementing a WMS so that you can see first-hand the ROI you receive due to reduced processing costs.
7. Reduced or Elimination or Errors
Businesses without a WMS often have people spending a lot of time on administrative duties, and as we all know, “to err is human.” A WMS reduces the human element considerably, which in turn, reduces the risk of error.
When picking, packing, and shipping, warehouse staff can just scan the barcodes and the WMS will let them know if the wrong product has been scanned. It will also automatically communicate inventory changes to other teams in real-time.
So, not only are errors reduced or eliminated, but you’re also less likely to have frustrated customers – and those pesky poor online reviews they’re known to leave.
WMS Advantages & Your Supply ChainA WMS plays a key role in supply chain management by managing order fulfillment processes, from receiving raw materials to shipping finished goods. Let’s say some raw materials are received improperly, or parts were misplaced within a warehouse; this could slow or stop the supply chain temporarily, costing the company money and potentially customers. A WMS keeps the whole operation in order, tracking inventory and making sure that goods are stored and sorted properly, as well as shipped and tracked accurately. It can even alert you to inventory oddities and spot potential problems before they become major issues. |
8 Key Features of a Warehouse Management System
Earlier we plowed through a laundry list of features any good WMS should have. Here’s a deeper look at each of those qualities. When shopping for a WMS system, its best that it includes all the following features.
1. Warehouse Design
Warehouses are not always organized well, wasting space and increasing time to execute essential tasks, such as picking, sorting, and order fulfillment. A good WMS will have the ability to optimize warehouse design.
It can be relied upon to optimize space usage, reduce unnecessary travel within the warehouse, and ensure high-demand items are placed in easily accessible locations. By doing this, it streamlines workflows, cuts down on labor costs, and speeds up order fulfillment, making the warehouse run more smoothly overall.
2. Inventory Tracking
A WMS platform needs to be able to track inventory data from barcode readers or other inventory tools such as radio frequency identification (RFID) tags, updating information in the software’s dashboard so the latest information is readily available to anyone with permissions.
3. Picking and Packing
Zone picking, wave picking, and batch picking can all be optimized by using a WMS. It may also offer warehouse workers lot zoning and task interleaving functions to guide their pick-and-pack process in the most efficient way.
4. Receiving and Put-away
This technology, available with some WMS platforms, quickens inventory put-away and retrieval through pick-to-light (PTL) or pick-to-voice (PTV) technology.
- PTL: Light displays are installed in shelving units and storage racks at every fixed pick location. The display units light up, one at a time, to show pickers which order line to pick.
- PTV: A computerized voice directs pickers to the right location via headset and instructs them on the quantity to be picked and any other instructions.
Handling 50+ Packages Daily? You Need This!Ensure every package is tracked and delivered with care and 99.9% accuracy |
5. Shipping
A WMS platform will send bills of lading (B/L) ahead of the shipment, generate packing lists and invoices for the shipment, and send advance shipment notifications to recipients.
6. Labor Management
Which employee needs to step it up – and which deserves a high-five? A WMS platform can monitor workers' performance by using key performance indicators (KPIs) that indicate who is performing above or below standards.
7. Yard and Dock Management
For larger operations, WMS platforms can assist truck drivers coming into a warehouse, guiding them to the right loading docks. Cross-docking and other functions of inbound and outbound logistics are additional features on some WMS platforms that companies may use as they begin to scale.
8. Reporting
WMS platforms can generate automatic reports which help managers analyze the performance of warehouse operations, warehouse employees, and more. This allows them to anticipate potential problems and find areas for improvement.
Choosing Your Warehouse Management System Software
For small and medium-sized Ecommerce businesses that need to watch their spending, it’s important to consider the costs you may incur when adopting a WMS. Cost of these costs include:
- Hardware
- Implementation
- Infrastructure
- IT labor
- Licensing fees
- Maintenance
- Software
Of course, it’s also important to remember that while there may be some upfront costs, over time a WMS will pay for itself, and then some.
In addition, many vendors selling cloud-based, Software-as-a-Service (SaaS), and integrable WMS solutions will often cover many of these costs themselves, so that your main responsibility will be paying for the software, licensing, and one-time implementation costs.
Read our in-depth guide on how to choose the right WMS for an ecommerce business.
Read more of our fulfillment and warehousing tips: |
Access Top WMS System Benefits with The Fulfillment Lab!
Warehouse management systems, or a WMS company, can do a lot for a business in terms of efficiency and accuracy, and many warehouses end up reaping rewards that they might have never seen coming. But, it can be difficult to choose which is right for your company and some can be quite complex.
If you’re looking to unload fulfillment duties to a fulfillment center, then you won’t need a WMS at all. When you store and ship your product through The Fulfillment Lab, you’ll have access to our proprietary Global Fulfillment Software (GFS™).
Unlike other WMS platforms, our technology allows you to see exactly what’s going on in our distribution centers where your products are stored, even if it’s in one of our facilities across the globe!
Not only does GFS provide the functionality of other high-end WMS software, but it also takes data from the front end of the sales funnel to gain more data on end-consumer purchases. It’s all done to help you grow your business and your knowledge of your customers.
Learn more about The Fulfillment Lab and our founder, or contact us to learn more about what we can do for you!