5 Key Ways to Improve Warehouse Efficiency
An efficient warehouse should always save your business money, space, and more. However, without taking steps to ensure optimal operations and efficiency, a warehouse can quickly become a source of frustration, errors, and lost revenue. Warehouse efficiency directly impacts productivity, customer satisfaction, and overall profitability.
Warehousing makes up 66% of all outsourced activities in a supply chain and the global 3PL warehousing market is expected to be worth $2.8 trillion by 2031. The need for reliable warehousing solutions is growing; warehouses that can operate efficiently, and enable their customers' businesses to operate seamlessly, will thrive.
“Warehousing efficiency management is not just about accurate inventory management and accurate order fulfillment. It’s about helping the companies that rely on warehousing providers deliver on the promises they make to their customers.” Rick Nelson, CEO, The Fulfillment Lab |
To stay on top of warehouse operations, and ensure productivity, profitability, and customer trust remain optimized, certain actions and steps should be taken, 12 of which we’ll discuss in today’s blog.
The top warehouse efficiency measures every warehouse needs to know (and we explore in this article) include:
- Warehouse layout optimization
- Warehouse automations
- Warehouse management systems (WMS)
- Safety first
- Using a fulfillment center
The Only 5 Warehouse Efficiency Tips You Need to Know
The importance of warehouse efficiency – and its impact on your bottom line – is something you shouldn’t overlook. How efficient a warehouse is determines how quickly it can move inventory in and out of its system – and the people wanting those goods aren’t willing to wait.
- 53% of customers will cancel a purchase if shipping is too slow.
- 65% of customers will change brands after a poor shipping experience.
Here are the 5 best ways you can begin improving warehouse efficiency and productivity. Some are easy to implement, and some can cost money, but all can help get your operation running like a well-oiled machine.
1. Optimize Your Warehouse Layout
Travel time can make up nearly 55% of the total picking time in a warehouse or distribution center. The first step to improving warehouse efficiency is optimizing your layout. A well-organized warehouse layout can significantly improve warehouse efficiency and reduce costs.
By carefully planning your warehouse layout, you can create a more efficient and productive environment, reducing unnecessary movements and ensuring that your operations run smoothly.
Design for Flow
Design your warehouse layout to support a logical flow of inventory from receiving to shipping. Position high-demand items closer to packing and shipping areas to speed up retrieval and reduce processing time. Use adjustable shelving and modular storage units to accommodate changes in inventory needs.
Utilize Vertical and Horizontal Space
Utilize tall storage units and efficient shelving systems to make the most of your warehouse's vertical and horizontal space. This approach can significantly increase your storage capacity without expanding your warehouse footprint, helping you store more inventory efficiently.
Zone Your Inventory
Group items into dedicated zones based on type, size, or demand to reduce travel time and streamline picking and storing processes. Label each zone clearly to help employees quickly find and store items.
Adjust for Seasonal Changes
Organize your inventory based on seasonal shifts. For example, store winter gear at the front of the warehouse during colder months and switch to summer must-haves as temperatures rise. This ensures that seasonal products are always accessible.
Supercharge Your Warehouse Operations Today!Book a free consultation with The Fulfillment Lab to get started. Let's Talk
|
2. Implement Warehouse Automations
Integrating automation into your warehouse operations can drastically improve efficiency, reduce human error, and increase productivity. Automation technologies streamline various tasks, from inventory management to order fulfillment.
Implementing the following automation technologies can transform your warehouse operations, making them more efficient, accurate, and reliable.
Automated Storage and Retrieval Systems (ASRS)
Smaller operations can function well enough with manual pickers, but as your warehouse grows, this approach can impact productivity. Consider this: The average order picker can pick 60-80 products per hour when routes are optimized; this rate can be increased to about 300 pieces per hour when using automation, such as sorters and conveyors.
While there are costs associated with adding automation, the order picking productivity will eventually pay for itself.
In fact, according to Robotics Business Review, automated and efficient warehouses are 76% more likely to boost inventory accuracy to 99% or higher, 36% more likely to have reduced labor costs an average of 3% per year, and 40% more likely to consistently ship within one day of an order's placement.
Use Barcode and RFID Systems
Implement barcode scanning and RFID systems to enhance inventory tracking and accuracy. These technologies ensure real-time updates on stock levels and locations, minimizing the risk of misplaced or miscounted items. Barcode scanners and RFID tags streamline the picking and packing processes, making inventory management more efficient.
Warehouse Drones
Utilize warehouse drones for inventory management and monitoring. Drones equipped with cameras and sensors can perform tasks like stock counting, goods transportation, and facility maintenance, improving overall efficiency.
3. Use a Warehouse Management System
Even if you’re not very tech savvy, the latest equipment can transform your business into a high efficiency warehouse. For example, a quality warehouse management system (WMS) can really streamline operations by helping ensure that goods and materials move along in the most efficient and cost-effective way.
It does this by keeping an eye on warehouse design, inventory tracking, picking and packing goods, receiving and put-away, shipping, labor management, yard and dock management, and reporting.
Keep Track of Inventory Like a Pro
A WMS gives you real-time visibility into your inventory, tracking goods from the moment they enter your warehouse until they ship out. This means fewer errors and more accurate stock levels, making your life a whole lot easier.
Smooth Out Picking and Packing
With a WMS, your workers get guided through the most efficient picking and packing routes. This cuts down the time spent searching for items and boosts order accuracy. Faster fulfillment means happier customers and a smoother operation.
Make Receiving and Put-Away a Breeze
A WMS can streamline the receiving process by quickly verifying incoming shipments and directing staff on where to store items. Efficient put-away processes mean your inventory gets stored in the best spots for easy retrieval later on.
Manage Labor and Resources Efficiently
A good WMS helps manage labor by assigning tasks based on worker availability and skill levels. It also tracks productivity and can point out where you might need more training or resources, essential information for improving warehouse efficiency.
Choose Cloud-Based for Flexibility
Using an on-premise legacy program, or “standalone WMS software”? These systems often require a lot more manual work and are prone to problems. Cloud-based solutions are considered the best type of WMS for just about any business, so it’s worth looking into one.
Plus, you can access them from anywhere, getting real-time updates and seamless integration with other software.
By integrating a robust WMS into your operations, you can boost efficiency, cut down on errors, and make sure everything runs like clockwork.
Pro-Tip: There are many other cool warehouse technologies available. For example, you could implement voice-enabled technology. Using headphones, these systems direct order pickers where to go, what to pick, and where to deliver it; it’s much more efficient than having them spend time reading order sheets or taking verbal direction from a manager. |
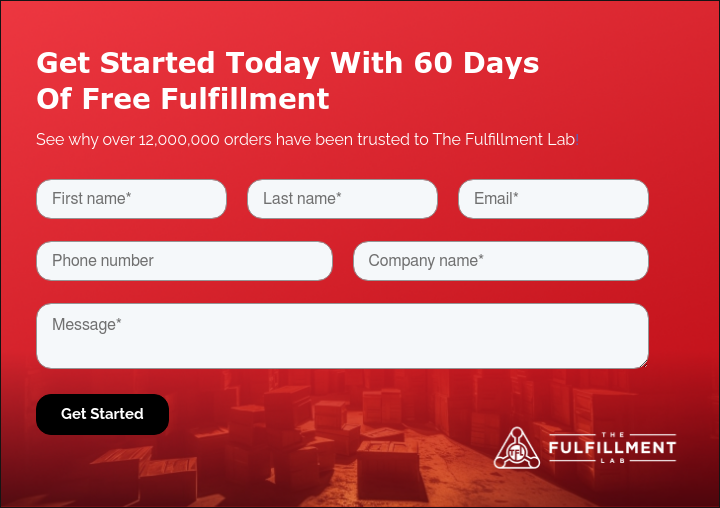
4. Never Skip Safety Measures
Unfortunately, warehouses have high rates of injury (about 1 in 20). The U.S. Bureau of Labor Statistics also reports that the rate of recordable illness and injury cases in the warehousing and storage sector is 5.1 out of every 100 workers.
If an employee gets injured, it can derail your whole operation; they are unable to work, causing productivity numbers and employee morale to go down.
Conduct Regular Safety Training
Keep your team up-to-date with regular safety training sessions. Cover everything from equipment usage to emergency procedures and safe lifting techniques. Well-informed employees are less likely to get injured, keeping everyone safe and operations running smoothly.
Implement Safety Audits
Regular safety audits are a must (and the law!). These help you spot potential hazards before they become real problems. By addressing issues early, you ensure a safer working environment for everyone.
Use Protective Equipment
Make sure everyone has access to and uses the necessary protective gear, like gloves, helmets, and safety vests. Proper use of this equipment can go a long way in preventing injuries.
Maintain Clear Aisles and Exits
Keep those warehouse aisles and exits clear! This prevents accidents and ensures quick evacuations if needed. Regularly check these areas to make sure they’re always free of obstructions.
Develop an Incident Response Plan
Have a solid incident response plan ready. This should include immediate medical attention, reporting procedures, and steps to prevent future incidents. Being prepared can make a big difference in how effectively you handle workplace accidents.
Other helpful warehouse management resources: |
5. Use a Fulfillment Center
Maybe you’d rather not be in the warehousing business after all! Then consider using a third-party logistics (3PL) fulfillment center. A fulfillment center handles the warehousing, picking, packing, and shipping of your products, along with returns management, customer service, and more. Some of the primary benefits they offer eCommerce businesses include:
- Cost savings. With a 3PL, the need for space—and the cost to rent or maintain it, along with overhead expenses—can be reduced. When it comes to shipping, 3PLs also have relationships with carriers which results in discounted pricing.
- Experience. Logistics are the speciality of a 3PL. By using a 3PL, you can tap into the knowledge of their experts and take advantage of the latest software and equipment that they’re utilizing.
- Global reach. Some eCommerce businesses feel bound by their location and remain local or national, unsure of international rules and regulations. Many 3PLs have a global reach, allowing businesses to bring their brand to a global audience.
- Customer service. Being able to handle returns, exchanges, and refunds is just as important as selling a product and a 3PL has the staff to do this.
- Scalability. As your business grows, space can become an issue and fulfilling orders fast enough can become difficult, resulting in shipping delays and disappointed customers. A 3PL can handle your inventory as you grow, housing and shipping it from one or multiple locations.
This is where The Fulfillment Lab can help.
Better Efficiency and Better Savings Start Here
Not only do we provide cost savings, experience, reach, customer service, and scalability, we also offer customized packaging solutions and an unbeatable, proprietary Global Fulfillment Software (GFS™). It easily integrates your eCommerce platform, and then you can begin to manage inventory, track orders, customize packages, and much more.
To learn more about how we can help your eCommerce business boost efficiency and improve customer experience as your end-to-end fulfillment partner, contact us today!